I've run into two issues, one of which represents another possible improvement to existing designs. Brad Litz mentioned that having the cooling vent in the throat might make noise, and that's a good point. But this represents an opportunity too. One of the things that plagues other large high-power basshorns is that the cooling vents are restricted. They are vented into relatively small rear chambers, and sometimes very near a wall so that flow is obstructed. So doing something to plumb those vents to outside air is probably a good idea.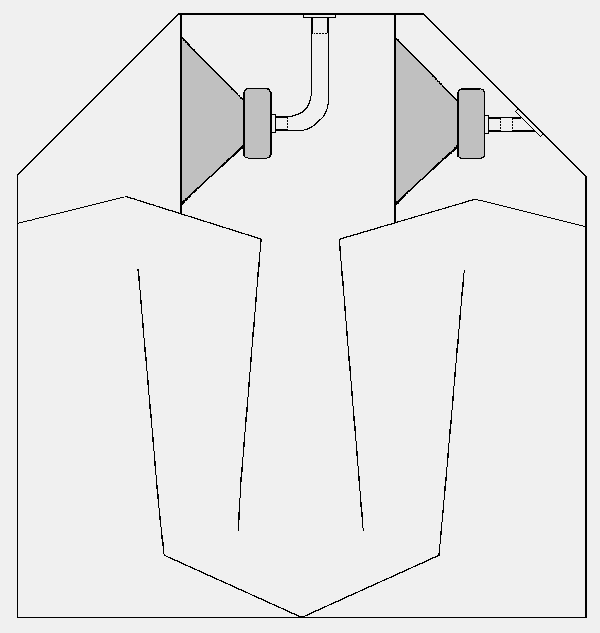
I'm thinking of doing something like shown above. I'll have the vent hole on the speakers fitted with a pipe fitting. It can be threaded, but I think a press fit is sufficient for no more pressure than we're talking about here. I'll also mount an exit fitting on the back of the cabinet and run a large rubber hose between them. Something like a heater hose, using the same diameter as the speaker vent. I'm thinking that this approach should really help keep the voice coils cool, and prevent unwanted noise at the same time. It's not a very difficult thing to do either, just a couple of fittings and a hose between them.
The other thing I'm thinking of is how to mount the drivers. They can have access panels or the entire motor assembly can be removable, and fasted with a series of studs, somthing like mounting the head of a car to the block. I'd probably make the horn complete all the way to the throat and then have a matching cutout in the plenum. The drivers can be accessed through that cutout. That would allow the entire assembly to be made solid and without access panels, which would probably make for a better seal. The two surfaces that meet would employ a rubber gasket, and they would be pulled together tightly using a series of fasteners like head bolts.